Float glass offers the quality of
plate glass combined with the lower production cost
traditionally associated with sheet glass
manufacturing. Float glass is virtually distortion
and defect free, making it ideal for various premium
glazing applications in buildings and homes or for
automotive glass along with hundreds of other glass
fabrications.
Float glass manufacturing is not unlike
the manufacturing of commodities like steel or plastic.
Each of the processes requires raw materials to be
weighed, mixed, melted at high temperatures, formed into
continuous ribbons, cooled and cut into a size that fits
its use.
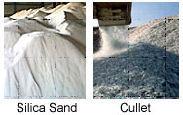
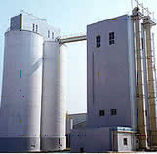
|
Float glass is made from a
combination of several ingredients such as sand,
soda ash, dolomite, limestone, salt cake, and
cullet.
The raw materials are received
and stocked in the silos or on/in the optional
storage areas. If the raw materials are stocked
in the optional storage areas they are then moved
as needed to the silos. The raw materials are
then drawn down from the silos for batch weighing
and mixing. Cullet, which is crushed glass from
edge trim of the cut lites or from broken cut
lites, is blended with the mixed batch to make
from up from 15% to 30% of each batch. The
mixture is then delivered to the melting furnace
by belt conveyor.
The batch house consists of,
silos, hoppers, conveyors, chutes, dust
collectors, and the necessary controls to
properly handle the raw materials and mixed
batch. The raw materials storage and handling is
designed to suit the types of glass which will be
produced along with the availability and cost of
the raw materials.
|
The mixed batch is
delivered from the batch house to the furnace
storage bin, by a belt conveyor system, where
it's stored and then feed into the furnace at a
controlled rate by the batch charger. As the
batch is feed into the furnace melter area it's
heated by the natural gas burners to
approximately 2900 degrees F. From the melter the
molten glass flows through the refiner then
through the waist area, where stirrers homogenize
the glass, then into the working end where the
glass is allowed to cool slowly to the proper
temperature for delivery to the float furnace.
The melting furnace
consists of refractory bricks and special shapes,
support and binding steel, insulation, a fossil
fuel firing system, temperature sensors and a
computerized process control system. The design
of the furnace is carefully made to meet the
plant's specific gross daily glass production
tonnage goals.
The insulation, special airflow
features, and combustion air heating enable the
furnace to operate at maximum fuel efficiency
with negligible pollutant emissions. The furnace
is sized and designed to provide high quality
glass with the smallest amount of energy per ton
of glass melted.
|
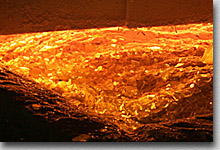
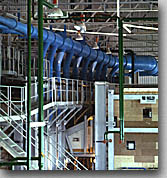
|
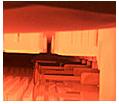
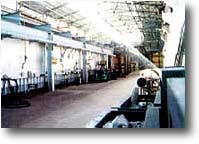
|
From the working end of
the melting furnace, the glass flows through the
canal area and then into the float furnace (tin
bath or float bath) onto molten tin. The float
furnace atmosphere is controlled by a mixture of
nitrogen and hydrogen gas to prevent the tin from
oxidizing.
The molten glass, which by now
has dropped to 2000 degrees F, forms a continuous
ribbon that floats on the molten tin. The desired
width and thickness is obtained through an
operator controlled program which sets the speed
of the annealing lehr and knurl machines. The
ribbon thickness can range from 2 to 12 mm. As
the continuous ribbon moves through the float
furnace its temperature is gradually reduced
allowing the glass to become flat and parallel.
The float furnace consists of
support steel, upper and lower welded steel
casings, a refractory liner, tin, electric
heating elements, an oxygen eliminating
atmosphere system, temperature sensors, and a
computerized process control system. Each
customer's float furnace is specifically designed
to respond to heat flow balance, desired ribbon
width, glass thickness, glass color and the gross
daily production tonnage.
|
The glass leaves the float furnace at about
1100 degrees F and enters the annealing lehr,
which controls the cooling of the glass. The
glass ribbon is carried through the lehr by a
series of rollers driven by motors and a
mechanical drive system. The temperature of the
glass is reduced according to a precise
time/temperature gradient profile, established
for each annealing lehr, to produce glass that
meets industry standards. The time/temperature
profile, for all of the glass thicknesses and
colors produced by the plant, is installed in the
computerized annealing lehr process control
system. The components of the annealing lehr
include a steel lined inner chamber and a steel
outer shell separated by insulation, steel alloy
and insulated steel rollers, a mechanical drive
system, air circulation fans and ducts, heating
elements, and temperature sensors and
computerized process control system. The design
of the annealing lehr is adapted to meet the
critical cool down requirements of each float
plant's gross daily production tonnage and glass
colors.
|
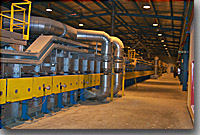 |
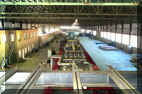 |
The cooled glass ribbon exits the annealing
lehr and is conveyed to the cutting area by a
system of rollers and drives linked to the lehr
drive system. The glass is scored by carbide
cutting wheels, parallel and perpendicular to the
ribbon travel, into sizes that meet the plant's
customer requirements. The scored glass ribbon is
then separated into lites for packaging by
unloading personnel or automatic equipment for
transfer to the wareroom for storage or shipment
to the customer. The cutting system consists of
steel support frames, a mechanical roll drive
system, "X "and "Y "cutting
system, a glass trim and scoring system, manual
unloading conveyors and/or semiautomatic or
automatic unload systems and a computerized
process control system.
|
|